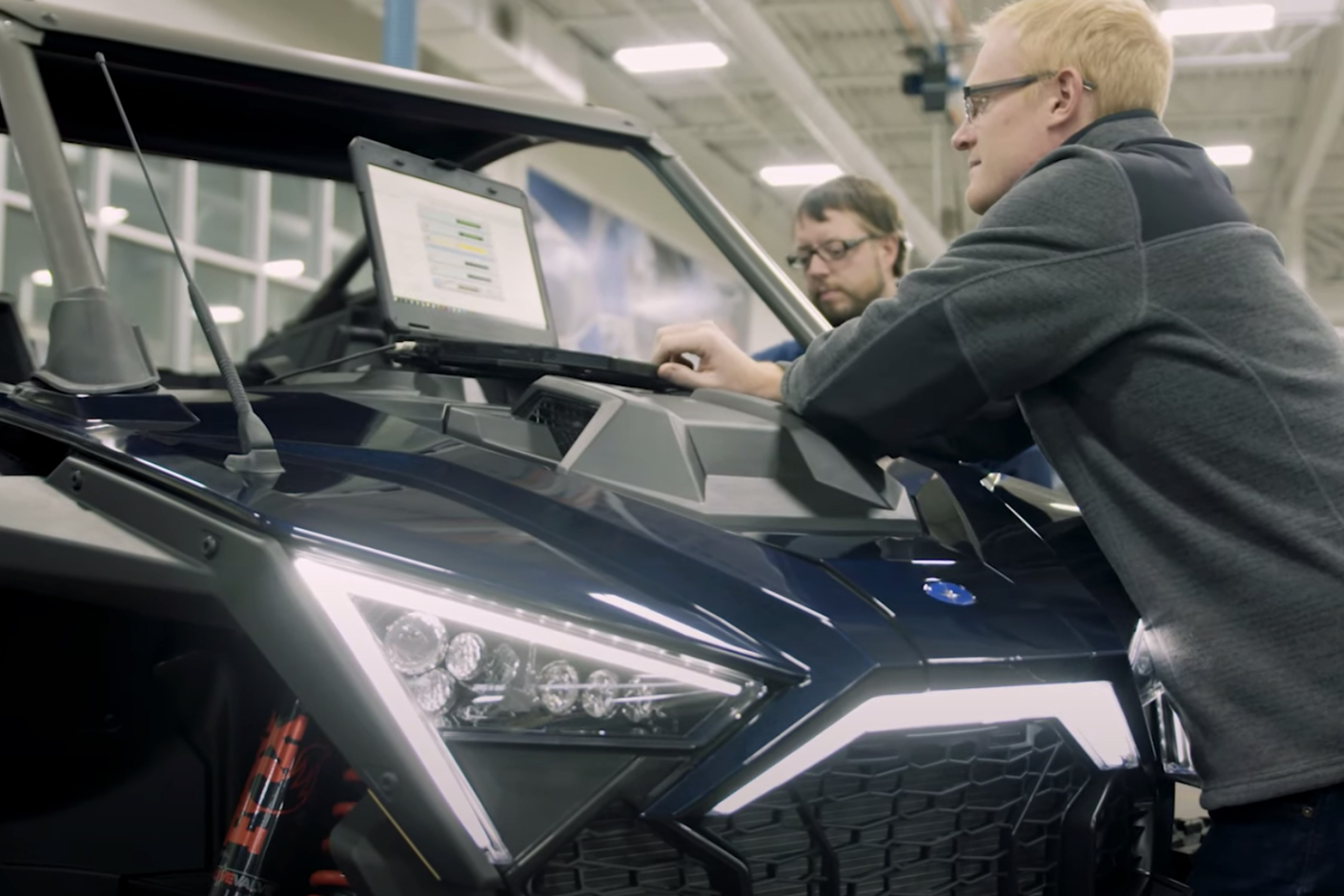
Polaris and FOX have been working together for years to create the perfect off-the-showroom suspension for UTVs for quite some time. We look at how the engineers at Polaris and FOX worked together to find the perfect tune of Live Valve X2 shocks on the RZR Pro R Ultimate and Turbo R Ultimate.
To start engineers did driving tests on chatter and whoop strips, using different handling maneuvers, and including custom data acquisition boxes to interact with the vehicle controller and calibration software. From there, they played with changing shims and drilling holes for the Internal Bypass between runs to dial in the ultimate tune.
“We evaluate that by driving it through our chatter strip here in Minnesota, over our whoop strip doing some handling maneuvers,” added Jonathon Graus, Polaris Electromechanical Systems Engineer. “We’re trying to throw some different electronics changes at it to see which way we need to go.”
“We’ve got these custom data acquisition boxes that interact with our vehicle controller and our calibration software,” explained Justin Anderson, Polaris Senior Electrical Technician. “We went out and collected some data, saw a little bit more roll angle in the corner than we’d usually look for and some acceleration spikes on airborne landing.”
“The Polaris Pro R has been one of the largest suspension development programs that Polaris has ever done, so we’ve had a lot of people working on this,” said Alex Scheuerell, Polaris Suspension Systems Engineering Manager.
If you haven’t seen them, the FOX 3.0 Live Valve X2 shocks are highly sophisticated and feature two electronic adjusters to control compression and rebound. Each adjuster is independently controlled by the semi-active Polaris DYNAMIX Dual Valve (DV).
Beyond being semi-active, what makes these shocks special are the unique oil flow paths for both compression and rebound. This means each adjustment is truly independent and does not affect the other.
For example, in the same moment the system can increase compression while decreasing rebound to maintain better support, traction, and comfort. It’s the intelligence behind DYNAMIX DV and Live Valve X2 that calibrates each shock separately on-the-fly.
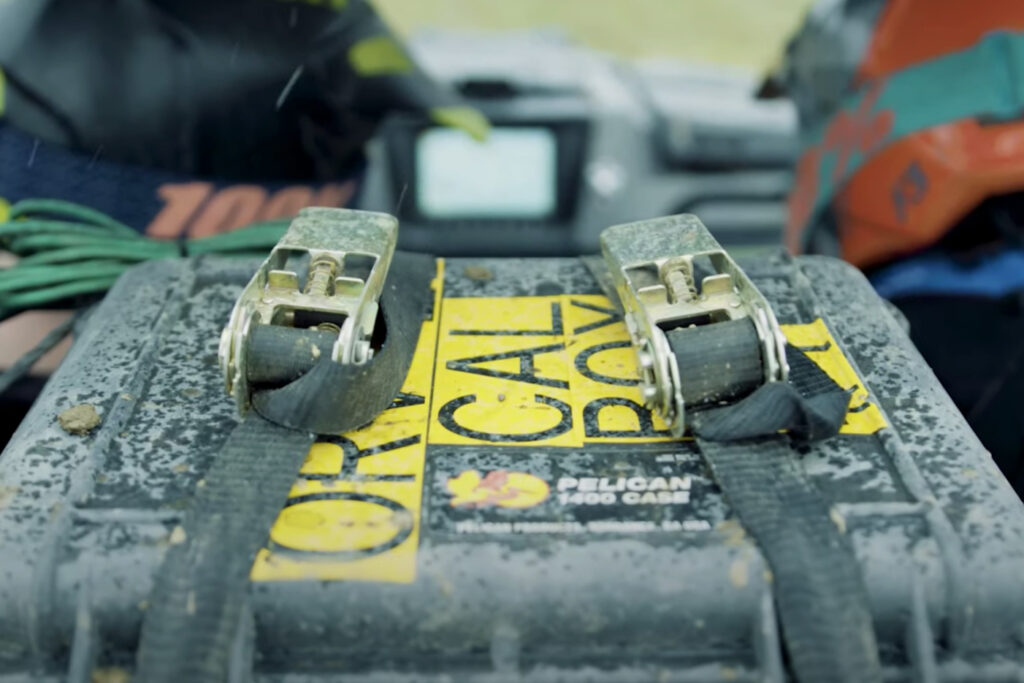
“We want to probably add some more valving to the shock, but in doing so, adding valving to the shock might introduce harshness,” Regan Woelfel, FOX Senior Engineering Manager, said. “We might want to drill the bodies of the Internal Bypass shocks to get some of that comfort back.”
In the front part of the FOX tuning trailer, Rick Strobel, Fox Powersports Race Manager, shows where the magic sauce or the science of changing shims and valving takes place. “We have all the testing tools to take our shocks apart,” he said. “We can go in and do the job and get right back out.”
“The control system on this vehicle has really come a long way since the original release of dynamics in 2017,” Graus explained. “During development we’d always talked about how it would’ve been awesome to have rebound control, so we made a prototype vehicle to prove out the technology to make sure independent rebound control added the performance that everyone was looking for.”
“FOX set us up with shocks that had independent compression and rebound damping. With that vehicle we got the workings of the control system ironed out,” Graus said. “Then, we upgraded it to a Turbo S and did a different set of development activities and learned further how to control the shocks even better. And then eventually that made it onto the Polaris Pro R.
“Independent compression and rebound damping control mean we can control the compression damping of the shock—including the shock getting shorter and the extension of the shock—with the rebound damping set to two different values at different times. This means our compression damping can be at 80 percent while our rebound damping can be at 20 percent. They’re infinitely variable in between there, and based on whatever the vehicle is doing, the vehicle can monitor the sensors and control the vehicle to have the optimized ride handling and traction for any situation.”
According to Anderson, Polaris uses shock position sensors to measure shock travel and look at shaft speeds, to see what the vehicle’s doing over a different terrain to understand what kind of damping changes they think would work.
“Once the control system was developed and ready to rock, we’ve really established a good way of tuning these shocks,” Graus explained. “Typically, we turn off all the electronics initially, and we set them to constant values, and we go out and we make sure that the hardware package is set up the way we want we’ll evaluate comfort or bottom-out at different settings.
“But we do that steady state so that we don’t have to have the confusion of also tuning the electronics at the same time. In a way, the electronics make the tuning more confusing, but it also makes it go really fast because if we want to do a damping change, we can make it in the electronics quick and check and make sure directionally that’s the right change. Then we go pull the shocks off and make the hardware change.”
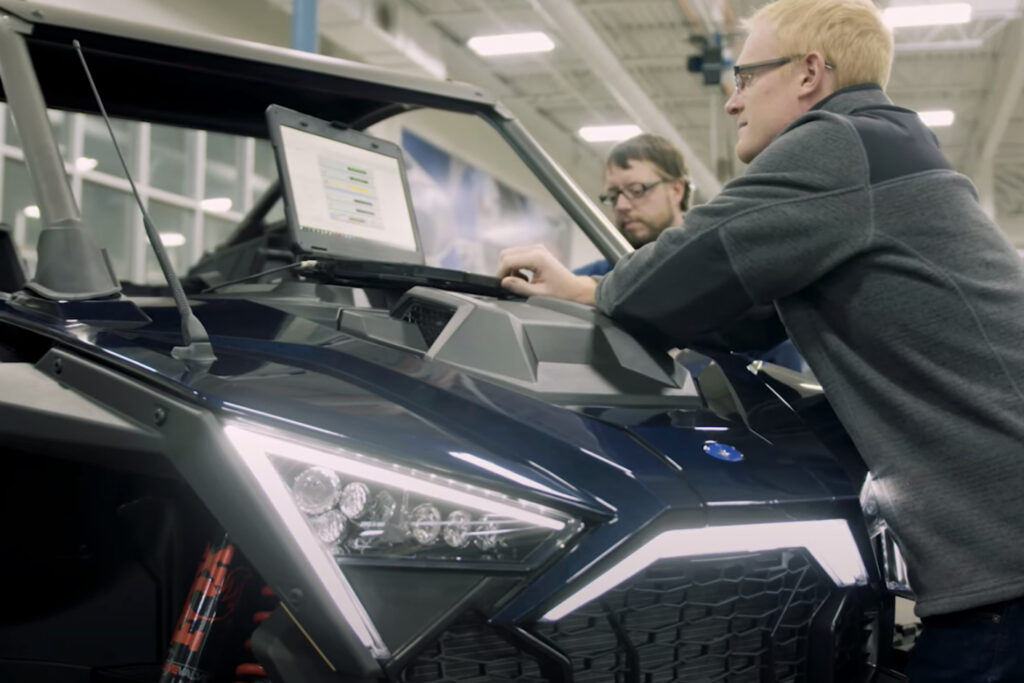
“We want to tune better, we want to tune faster, and we want to have more information while we’re out tuning,” Strobel said. “When we put instrumentation on the vehicles and we get all that information, now we need to bring it back inside of the trailer, go through it, understand what the vehicle’s doing in the field. Then we go to our dyno.
“We can look at the shock. We can see what our shock’s doing at the exact time of what the data acquisition is showing us and make the changes to the shock. We then put it back on the vehicle and ride it again.”
According to Graus, once Polaris has the hardware set, the electronics group and the hardware group are kind of working in parallel.
“We’ve got two different vehicles and we’re getting the vehicle detections working and the vehicle model’s working so that this vehicle knows when it’s cornering,” he explained. “And it knows when it’s braking, it knows when it’s airborne and we spend some time getting those damping values in the right spot.
In Baja mode, we’ve got the right compression and rebound damping. And when you corner, it comes on to these values and that provides the cornering control that we like or the traction that we like. Once we’ve got a preliminary version of the electronics on that, it’s a lot of fine tuning on individual things where we ran this mode through these events, and we didn’t like this, but then the other mode works this way, so we make changes to the electronics to help with that. Or we can’t make the changes to the electronics because it hurts some other things, so we go back after the hardware.”
“We’re happy to have FOX out here at our test facility today,” Graus said with a smile. “When we’re all working together this stuff really goes fast. We got all the brains in one spot, and we can really get this vehicle riding and handling the way that we want.
“My role in this project has been pretty awesome the last few years, because FOX and Polaris are both willing to allow us to develop this technology and take it to the next step for the consumer. I’m looking forward to getting this out into the public so consumers can ride it, feel it, and understand how much of an improvement over previous models this is.”
For more information on FOX and its products, be sure to check out its website.